Cobalt is a shiny steel-gray metal, relatively hard and brittle, ferromagnetic, and similar to iron and nickel in hardness, tensile strength, mechanical properties, thermodynamic properties, and electrochemical behavior. The magnetism disappears when heated to 1150℃. The fine metallic cobalt powder produced by hydrogen reduction process can spontaneously ignite into cobalt oxide in the air. Oxidation occurs at high temperatures. When heated, cobalt reacts violently with oxygen, sulfur, chlorine, bromine, etc., to form corresponding compounds. Cobalt is soluble in dilute acids and is passivated in fuming nitric acid by forming an oxide film. Cobalt is slowly etched by hydrofluoric acid, ammonia and sodium hydroxide. Cobalt is an important raw material for the production of heat-resistant alloys, hard alloys, anti-corrosion alloys, magnetic alloys and various cobalt salts. Cobalt is an amphoteric metal.
The physical and chemical properties of cobalt determine that it is an important raw material for the production of heat-resistant alloys, cemented carbide, anti-corrosion alloys, magnetic alloys and various cobalt salts. Cobalt-based alloy or cobalt-containing alloy steel is used as blades, impellers, conduits, jet engines, rocket engines, missile components and various high-load heat-resistant components in chemical equipment and important metal materials in the atomic energy industry. Cobalt as a binder in powder metallurgy can ensure that cemented carbide has a certain toughness. Magnetic alloys are indispensable materials in modern electronic and electromechanical industries, used to manufacture various components of acoustic, optical, electrical and magnetic equipment. Cobalt is also an important component of permanent magnetic alloys. In the chemical industry, cobalt is used in addition to superalloys and anti-corrosion alloys, but also for colored glass, pigments, enamel and catalysts, desiccant and so on. In addition, cobalt consumption has the highest growth rate in the battery sector.
The metal cobalt is mainly used to make alloys. Cobalt base alloy is a general term for one or several alloys made of cobalt and chromium, tungsten, iron and nickel. The tool steel containing a certain amount of cobalt can significantly improve the wear resistance and cutting performance of steel. Starlite carbide containing more than 50% cobalt will not lose its original hardness even if heated to 1000°C, and now this carbide has become the most important material used between gold-containing cutting tools and aluminum. In this material, cobalt combines other metal carbide grains in the alloy composition, so that the alloy has higher toughness and reduces the sensitivity to impact. This alloy is fused and welded on the surface of the parts, which can increase the life of the parts by 3 to 7 times. The most widely used alloys in aerospace technology are nickel-based alloys, and cobalt-based alloys can also be used, but the "strength mechanism" of the two alloys is different. The strength of nickel-based alloys containing titanium and aluminum is high because of the formation of a phase hardening agent composed of NiAl(Ti), when the operating temperature is high, the phase hardening agent particles are transferred to the solid solution, then the alloy quickly loses strength. The heat resistance of cobalt-based alloys is due to the formation of refractory carbides, which are not easy to turn into solid solutions, and the diffusion activity is small. When the temperature is above 1038 ° C, the advantages of cobalt-based alloys are fully displayed. For high-efficiency, high-temperature engines, cobalt-based alloys are just right.
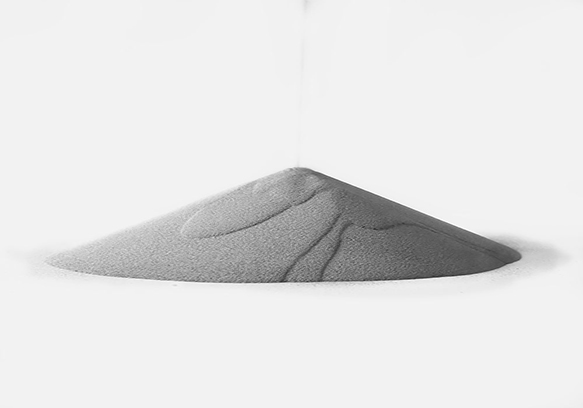
Chengdu Huarui Industrial Co., Ltd.
Email: sales.sup1@cdhrmetal.com
Phone: +86-28-86799441
Post time: Jun-07-2023